클린룸(Clean Room)이란 공기 중의 부유 미립자가 규정된 청정도 이하로 관리되고 그 공간에 공급되는 재료에 대해서도 요구되는 청정도가 유지되며 온도·습도 등 환경에 대해서도 관리할 수 있도록 만들어진 구역이나 공간을 말한다.
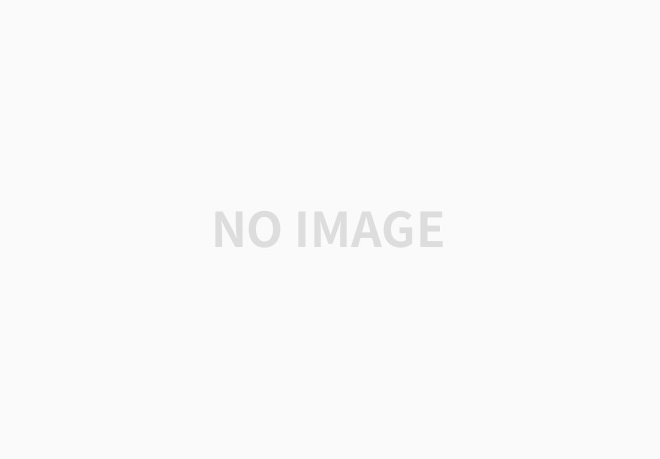
클린룸(Clean Room) 폭발위험장소 설정(1)
반도체와 FPD(Flat Panel Display)산업의 클린룸(Clean Room) 내에 설치되는 FAB 장비는 일반 화학설비와 구조적 형태와 기술적 차이를 가지고 있어, 일반적인 화학설비와는 달리, 화학물질을 취급하는 부분과 일종의 기계적인 제조 및 조립하는 장치를 포함하여 해당 장비의 내부 전체를 폭발위험장소로 산정하기에는 현재의 기술적인 상황으로 어려움이 많다.
클린룸(Clean Room)의 정의
공기 중의 부유 미립자가 규정된 청정도 이하로 관리되고 그 공간에 공급되는 재료에 대해서도 요구되는 청정도가 유지되며 온도·습도 등 환경에 대해서도 관리할 수 있도록 만들어진 구역이나 공간을 말하며, 먼지나 기타의 미립자(Particle)를 마이크로 필터로 제거하여 청정도를 유지하는것이 클린룸이며 제약회사, 전기전자제품, 반도체, FPD, 정밀 기계공장 등에서 활용된다.
클린룸을 구성하기 위한 기본 요구사항은 발생된 미립자를 제거, 미립자 발생 방지, 미립자의 누적 방지, 미립자의 침입 방지, 필요한 온도·습도 및 실내 압력유지, 청정한 공기 송풍이다.
클린룸의 등급과 환기
클린룸은 반도체, FPD 등 첨단산업에서 제품의 생산수율, 공정의 정밀화, 미소화, 고품질화 및 높은 신뢰성이 요구되고 있는 ICR(Industrial clean room)이 있으며, 클린룸 내 환기설비의 환기 횟수에 따라서 청정도 Class 100에서 Class 100,000까지 구분하고 있으며, 여기서의 환기 횟수는 폭발위험범위를 계산하는데 고려하여야 할 중요한 Factor로 작용할 수 있다.
폭발과 방폭 이론
전기방폭의 기본 개념과 누출원 및 환기특성, 폭발위험장소에서의 전기/계장기계·기구(이하 "전기설비"라 함) 선정과 관련된 이론에 대하여 기술한다.
폭발위험장소 설정에 관련된 이론, 즉 폭발방지의 기본개념과 원리, 폭발위험분위기 생성의 방지 메커니즘과 위험성 그리고 전기설비의 방폭화 방법과 폭발위험장소의 누출량의 산정과 위험범위에 영향을 미치는 환기특성 및 환기량 평가 산정하는 방법, 위험반경과 폭발위험장소 구분하는 방법에 대하여 검토한다.
"폭발위험장소(Hazardous area)"는 "전기설비를 선정·설치·사용함에 있어 특별한 주의를 요구하는 폭발성 가스위험분위기가 조성되거나 조성될 우려가 있는 장소"를 말하며, 이러한 장소는 위험분위기의 발생 가능성, 즉 폭발성 가스분위기의 생성빈도와 지속시간에 따라 0종 장소, 1종 장소, 2종 장소 등으로 나누고 그 위험범위를 설정하는 것이다.
폭발위험장소의 효과적인 설정
FAB 장비는 클린룸의 환경특성과 장비 자체의 특수성을 고려하여 다음의 여러 조건을 반영하여 폭발위험장소를 선정하면 설비에 대한 안전성 확보뿐만 아니라 폭발위험범위의 최소화, 최적화를 통하여 방폭기기의 적용 최소화를 가져올 수가 있을 것이다.
1. 클린룸의 환기특성(환기와 희석)
클린룸은 전체 환기를 지속실시하고 장비단에서의 기류가 규칙적으로 형성된다. 따라서 위험물질이 미량으로 누출 되더라도 환기가 되고 희석이 되어 위험분위기를 만들 수 있는 환경조건에 도달하기가 거의 불가능하다.
2. 개별 FAB 장비의 국소적인 배기 특성(강제 배기)
개별장비의 공정조건을 맞추고 이물(Particle) 제거, 세정·건조 및 코팅 과정에서 발생되는 VOC의 배출 등을 위하여 클린룸 전체 환기 외에 각 장비에서는 ME(Mini environment)를 구성하여 국소배기를 가동하고 있어 강제환기가 상시 이루어지고 있다.
3. FAB 장비의 특수성
(1) 진공을 사용하는 진공장비는 인화성 가스가 누출될 수 있는 확률을 거의 "0"에 가깝게 운전조건을 유지하고 있으며, 사용하는 인화성가스의 양 자체도 수 g 단위이다.
가스나 액체가 증발되면 즉시 배기를 통하여 VOC나 RTO를 통하여 처리되고 있다.
Gas를 공급하는 공급장치 및 배관들의 경우 금속 가스켓 양면 접속 피팅이라는 VCR(Vacuum coupling radiation) 피팅방식으로 시공되고 있다. VCR 피팅 부품은 고순도 제품의 밀폐유지, 진공에서 양압까지의 누출이 없는 고신뢰성 제품이여야 하므로 제품에 대한 설계기준과 시험검사 기준이 제시되고 있으며 여러 시험방법으로 기밀성, 신뢰성에 대한 품질보증을 하고 있다.
따라서 이와 같이 특수한 사례의 경우는 VCR 피팅에 의한 연결부위는 통상적으로 정의되는 2차 누출원(플렌지 접합부)과는 기술적으로 차이가 있다는 인식이 필요하다.
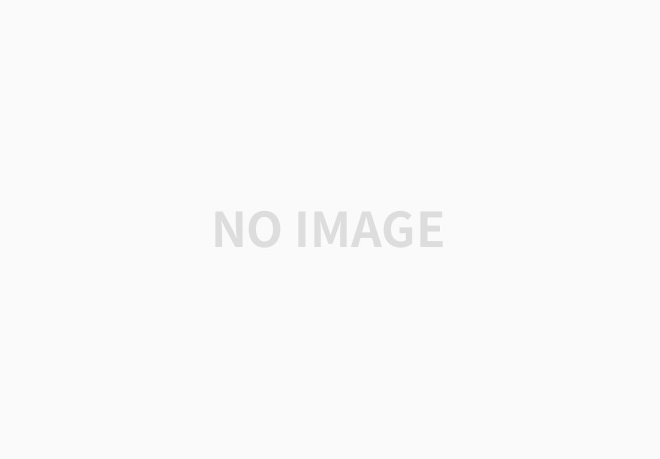
<그림 1> Picture of VCR Fitting
(2) Gas/Chemical 공급실, FAB 장비의 전 구간에 걸쳐 가스감지기 또는 누액감지기가 설치되어 상시 누출에 대한 감시를 하고 있으며, 누출시 인터록(Interlock)이 설정되어 있어 긴급차단밸브(ESOV) 차단이나 설비 운전정지 상태 등으로 설비를 안전한 상태로 변경하게 된다. 인화성액체의 배관은 Tubing을 통하여 이중배관으로 구성되어 있다.
4. 폭발위험을 줄이기 위한 대책의 적용
위험물질 누출에 의한 폭발위험장소의 범위를 축소하거나 제거하기 위한 다음과 같은 대책이 필요하다.
<표 1> Measures of eliminate explosion risk
구분 | 주요 대책 |
공정 조건 | 1. 위험물질의 대체 또는 사용 양의 감소 (폭발위험분위기 조성의 물질 소량기준 설정) 2. 위험물질의 농도 제한(저농도화-폭발하한계 25%미만) 3. 공정 조건의 불활성화(Inerting) |
장비 설계·구조 | 1. 위험물질이 누출되지 않는 폐쇄적 구조/이중화 구조 2. 단위장비별 국소배기 (배기 시스템의 모니터링 기능을 갖추고 설정 배기압 이탈시 경보-Interlock system) |
누출 회피·감소 | 1. 위험물질이 누출되지 않는 구조적 설계 및 시공 2. 장치 및 배관 연결부 최소화 3. 배관 및 이음매(개스킷, 접합부, 패킹) 연결 소재의 내마모성과 견고성, 기밀성 유지 4. 소재의 접합성(내마모성, 내부식성) |
감시 기능 | 1. 가스감지기, 누액감지기의 Interlock system 2. 국소 또는 강제배기 가동 및 유량(정압) 유지 모니터링과 Interlock |
Reference : 우인성 등, 반도체·FPD 제조설비와 클린룸의 RISK 최소화를 위한 폭발위험장소 설정 모델링에 관한 연구
'공정 및 화공안전 > 폭발위험장소 관리' 카테고리의 다른 글
천연가스(NG) 보일러실 위험장소 설정(1) (2) | 2023.05.23 |
---|---|
클린룸(Clean Room) 폭발위험장소 설정(2) (0) | 2023.03.24 |
폭발분위기의 회피 또는 감소 (0) | 2023.03.21 |
KS C IEC-60079-10-1: 2012 vs. 2015 차이 (0) | 2023.03.18 |
KGS GC101 계산 사례(프로판) (0) | 2023.03.18 |
댓글