화학공정은 공장의 선정 시부터 건설 및 생산에 이르기까지 치밀한 설계와 계획이 필요하다. 이것이 잘못되었을 경우 안전과 환경문제를 야기시키며 결과적으로 사회에 혼란을 가져올 수도 있다. 이를 역으로 생각하면, 설계단계에서부터 계획을 잘 세우면 생산 단가를 낮출 수 있을 뿐 아니라 안전과 환경의 문제를 근본적으로 해결할 수 있다. 이러한 근본적으로 안전(inherently safe technology)하고 청정(clean technology)한 공정을 설계하고 계획하는 것이 공정설계의 주된 역할이다.
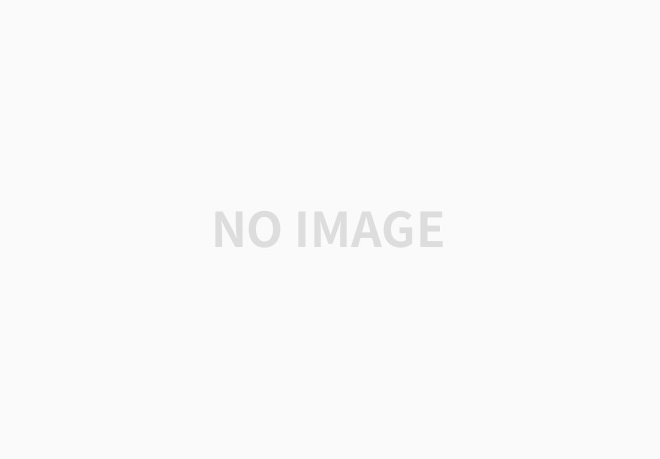
화학공정 안전과 설계
화학공정 안전이란?
화학공정 안전은 화학물질을 대량으로 제조, 취급, 저장하는 동안의 사고 방지에 중점을 두고 있다. 특히, 제조 시의 사고는 화학 반응이 일어나는 동안 또는 폭주 반응으로 인해 위험한 물질 및 에너지가 환경으로 의도치 않게 방출되는 것을 말한다.
화학 산업에서, 공정 안전 사고는 다음과 같이 여러 가지 이유로 발생한다.
- 정보 누락
- 사용자 교육 부족
- 기술적 결함
- 사람의 실수
- 우연한 사고의 연속
기능 장애, 사람의 실수 그리고 가능한 모든 부반응 및 파라미터가 관련된 화학작용에 대한 이해 부족은 사고가 발생하는 가장 빈번한 원인이 된다.
위험 분석과 함께 위험요소 및 위험을 식별하고 이해하면, 분해를 촉발시키는 위험을 평가하여 반응 시 적절하게 제어할 수 있다.
화학 공정 안전의 중요성
간단히 말하자면, 시험 또는 제조 규모 단계에서 사고를 예방하는 것이다. 일반적으로, 제품은 소량의 물질로 극한의 조건에서 시간에 쫓기면서 개발된다. 몇 년이 지나면, 화학 공정의 수가 많아지고, 공장은 복잡해지며, 화학반응은 독성이 강해지고, 운영 환경은 더욱 위험해진다. 이런 점 때문에, 사고가 발생하면 규제 당국 및 사회는 더욱 민감해지고 규제 중심으로 생각하게 된다. 이런 트렌드의 영향을 받아, 종합 화학 공정 안전을 개선시키고 본질적으로 안전한 화학 공정 및 화학물질의 제조를 보장하는 컨셉을 개발해야 한다. 본질 안전 설계는 화학적 위험성을 제어한다기보다는 예방하는 것이다.
안전한 운전을 위해, 공정 및 공정 위험을 분명하게 이해해야 한다.
철저한 화학 공정 안전 연구는 폭주 반응을 방지할 뿐만 아니라, 공장의 손상 또는 파괴, 인명 상해 또는 환경 오염을 방지할 수 있다.
화학 공정 안전 연구의 목적은 잠재된 모든 위험요소, 영향 및 결과를 종합적으로 파악하기 위한 것이다.
화학 공장에서 사고의 결과는 공장의 소소한 손상부터 끔찍한 인명 상해 또는 사망, 공장의 심각한 파손 또는 파괴, 재난 수준의 환경 손상 그리고 주변 지역의 사망자 발생에 이르기까지 다양하다. 규모를 달리하는 사고는 회사의 명성과 경제적 손실에 매우 큰 영향을 주게 된다.
이 모든 것들이 화학 공정 안전에 대한 투자가 필요한 정당한 이유이다.
공정설계와 안전
화학공장의 공정설계단계에서 고려되어야 할 안전과 관련된 사항을 요약하면 다음과 같다.
- 각종 원료, 중간제품, 완제품의 물성조사 :
인화점, 발화온도, 폭발한계, 금수성물질 여부, 타물질과 혼합 시 이상반응 여부, 분해온도, 부식성, 증기압, 치사량 또는 허용농도, 증기 밀도 등
- 운전 및 설계조건의 결정 :
운전온도, 압력, 유속 등
- 운전(제어) 방법의 결정 :
온도 조절의 자동 또는 수동, 압력 조절 방법, 유량 조절 방법, 원료 계량 및 투입 방법 등
- 각 설비별 안전장치의 설치여부 검토 :
안전밸브, 파열판, check valve, 긴급 차단밸브, 긴급 방출 밸브, flame arrester, scrubber, 배기 및 환기설비, flare stack, 가스검지 및 경보설비, 공기흡입 검지기(산소 검지기) 등
- 각 설비별 재질 검토 :
반응기, 증류탑, 열교환기 등 압력용기, 배관 밸브류 및 gasket 등
- 이상상태 발생 시 대책 :
유해위험물질 누출 시, 온도 및 압력 상승 시, 등
운전 및 설계조건 결정 시 안전기준
공정설계 중에서도 가장 중요한 안전상의 조치는 안전하게 운전할 수 있도록 운전조건을 결정하고 그에 따른 설계조건을 결정하는 것이다.
⊙ 운전조건의 결정기준
- 가연성 물질을 취급하는 공정은 폭발범위에서의 운전을 금한다.
- 폭발범위 내에서 또는 그 부근에서 불가피하게 운전해야 할 경우에는 농도계를 설치해야 하고 불활성 가스 주입설비, 폭발 제어장치(압력 자동 방출장치)를 설치해야 한다.
- 운전조건은 다음 3가지로 구분하여 표시되어야 한다.
. 최저 운전온도, 압력, 유량(minimum working condition)
. 통상 운전온도, 압력, 유량(normal working condition)
. 최대 운전온도, 압력, 유량(maximum working condition)
- 펌프류 등의 유체 이송기계는 실제 운전 시 유량(용량) 변동이 심하고, 다양하게 운전될 수 있어야 하므로 양정(head)과 유량을 동시에 감안한 운전 범위가 설정되어야 한다.
⊙ 설계조건의 결정기준
- 설계온도 : 운전 시 최고 사용 온도에 20℃(또는 30℃)를 가산한 수치를 설계 온도로 결정한다.
- 설계압력 : 사용압력(working pressure)의 1.1배 또는 사용압력에 1.8kg/㎠을 가산한 수치 중 큰 것을 설계압력으로 정한다.
- 유속 : 저장탱크에 가연성 물질이 인입될 때의 속도는 1m/sec 이하로 해야 하고(API 기준) 배관의 크기별 안전 유속은 다음 표와 같다.
<표 1> 가연성 물질 관경에 따른 안전유속(독일)
배관의 호칭(inch) | 1 | 2 | 4 | 8 | 16 | 24 |
관경(mm) | 25 | 50 | 100 | 200 | 400 | 600 |
제한속도(m/sec) | 3.5 | 3 | 2.5 | 1.8 | 1.3 | 1.0 |
일반적으로 배관의 유속은 1m/sec에서 3m/sec로 하는 것이 국제적인 통례이고 이것은 경제적 측면과 안전성(errosion, 마모에 의한 부식)을 고려하여 정해진 경험적인 수치이다.
운전(제어) 방법의 결정
공정설계 중 핵심적인 기술은 생산작업(운전)을 어떻게 하면 경제적이고 안전하게 할 수 있느냐 하는 운전방법을 결정하는 기술이다. 이 문제는 생산제품, 원료의 특성, 생산공정의 복잡성, 운전자의 기술 수준 등 여러 가지 요인에 의해 결정되는 사항이기 때문에 일반적으로 기준을 정하기는 어렵다. 그러나 통상적인 개념에서 일반적인 기준을 명시하면 다음과 같다.
- 자체적으로 발열반응(exothermic reaction)을 일으키는 공정의 반응기는 온도 지시 기록계 및 경보기가 설치되어야 한다.
- 흡열 반응(endothermic reaction)에 있어서 스팀 등을 공급하여 온도를 일정하게 유지해야 할 경우에는 스팀량을 자동 조절할 수 있도록 하고 온도 지시 및 기록계가 설치되어야 한다.
- 반응 또는 운전 압력이 3 psig 이상인 모든 반응기, 탑조류, 열교환기, 탱크류 등에는 압력계가 설치되어야 한다.
- 운전압력이 3psig 이상인 반응기에는 압력 지시 및 기록계와 경보기가 설치되어야 한다.
- 위험물질을 취급하는 화학설비(반응기, 탑조류, 열교환기, 탱크류 등)에서 내압이 변경될 수 있을 경우에는 압력조절장치를 설치해야 한다.
- 부반응을 동반할 수 있는 화학설비에는 자동 긴급 방출장치 또는 차단장치를 설치해야 한다.
- 반응물질을 일정한 비율로 공급할 경우에는 유량 또는 혼합비를 조정할 수 있는 연동장치를 설치해야 한다.
- 발열반응을 일으키는 반응기에서 냉각수 등이 차단될 경우를 대비하여 자동 운전 정지 또는 긴급 냉각이 가능하도록 해야 한다.
- 압력의 상승에 의해 반응속도가 중가 할 경우에는 자동 압력방출장치를 설치해야 한다.
- 액위의 상승 또는 하락에 의해 운전상의 위험이 있을 경우 자동 액위 제어 설비를 해야 한다.
반응의 위험성
화학반응, 진행 경과 그리고 부산물 및 불순물의 형성은 일반적으로 온도, pH, 압력, 반응 속도, 교반, 혼합, 용매 유형, 촉매제 등 파라미터에 의해 제어된다.
공정설계에서, 화학반응 동역학 같은 파라미터 외에도 최대 열 방출, 열 및 미반응 물질의 누적, 열 및 질량 전달, 점성 변화, 파울링, 침전 또는 기체 방출도 고려해야 한다.
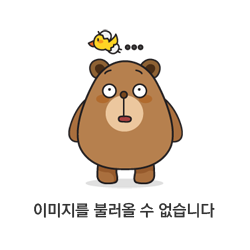
<그림 1> 화학반응 및 제어 개념
화학반응을 일으키는 공정은 통상적으로 높은 온도와 압력에서 이루어지기 때문에 공정설계에서 안전상의 조치를 특별히 고려해야 할 부분은 반응(reaction)이라 볼 수 있다. 따라서 반응 공정 중에서도 특수한 온도와 압력에서 운전되고, 취급 물질이 위험한 반응 설비인 경우에도 법적으로 안전상의 조치를 하도록 규제되어야 할 것이다. 이러한 안전상의 조치는 공정설계단계에서 엄밀히 적용되어야 하며 그 기능이 운전 중에 중지되거나 훼손되지 않도록 감시·확인될 수 있어야 한다.
이와 같이 위험한 반응기로 볼 수 있는 것은 심한 발열반응을 일으키거나 이상반응 또는 2차 반응을 일으켜 폭발 가능성이 많은 것을 말하고 있다.
이상과 같은 반응기에는 특별한 안전상의 조치를 하여야 하는데 그 내용은 다음과 같다.
- 내부 반응 상태 감시장치 :
온도, 압력, 지시 기록 및 경보설비는 물론 반응기 내부의 상태를 검지할 수 있는 장치가 필요함
- 이상상태 발생 방지조치 :
. 원재료의 공급 차단 및 내용물 방출장치(자동 차단 및 방출이 가능하도록 되어야 함)
. 불활성 가스 공급장치 및 냉각수 긴급 공급장치 또는 반응억지제 투입설비
. 공장의 긴급 자동 차단장치
. 내용물의 긴급 이송설비(펌프, 배관, 저장 등의 설비)
그 외 발열반응을 행하는 반응기, 폭발 범위 내에서 운전되는 증류탑 등의 화학설비 그리고 위험물의 분해 온도 또는 발화 온도 이상의 열매체를 사용하는 화학설비 및 기타 폭발성 물질을 생성하는 화학설비는 안전상의 조치를 해야 하며, 이 경우 반응기 내부 감시장치를 제외시킬 수 있다.(그러나 온도, 압력 등의 지시 기록 경보 등의 계장설비는 당연히 설치해야 함)
Reference : Daniel A. Crowl/Joseph F. Louvar, Chemical Process Safety Fundamentals with Applications
https://www.mt.com/kr/ko/home/application
'공학 기술 > 공장설계' 카테고리의 다른 글
증류탑 설계 시 고려사항 (0) | 2022.02.17 |
---|---|
Fail-Safe Position 선정 (2) | 2022.01.13 |
공정 설계(process design) 개요 (0) | 2021.12.29 |
릴리프 시나리오 개발 (0) | 2021.12.25 |
릴리프장치 설치 지침 (0) | 2021.12.24 |
댓글